Health and Sanitation System
Daido Steel continuously implements the health and sanitation program for employees in cooperation with Medical institutions and the health insurance association.
Health Guidance System
Daido Steel is promoting the health and sanitation activities as well as good health of workers, using a staff of industrial health insurance experts. Clinics are set up at core business sites, where so-called health keepers take measures to reduce low-back pain and provide guidance to all employees after regular health check-ups.
In collaboration with the health insurance association, a health promotion program is being implemented through a variety of activities such as walking events, and diet education involving the introduction of healthy menus and a balanced diet.
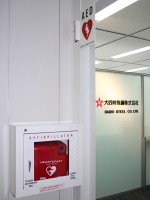
AED*and Emergency Lifesaving Training Course
Daido Steel has set up AED (Automated External Defibrillator) equipment at 11 work facilities and provides lifesaving courses for staff members.
AED*(Automated External Defibrillator): This medical equipment is designed to restore heart activity by administering an electric shock.
Work-Life Harmonization
Daido Steel considers that the development of the company is closely linked with the fact that each employee who maintains a work-life balance brings about a positive cycle of a fulfilling work and home life. With that aim in mind, Daido Steel incorporates various systems to improve the work environment.
Education for Employees
To develop human resources that will put the Code of Conduct into practice and realize our management philosophy, we have adopted a human resource development policy of “promoting employee autonomy and developing human resources who will learn (grow) autonomously with a high sense of ethics, and persist in their challenges.” We engage in employee development based on our expectations for each grade summarized in the skills development guidebook to the right, knowledge acquired off-the-job, and skills.
Development of Professional Human Resources
Employees acquired the required knowledge and skills at each level based on our life education system so that they can grow in stages into manufacturing professionals.
Safety
Daido Steel cooperates in three-way activities with labor and management under the basic policy that “Safety comes before everything.”
Security Management System
Daido Steel always has the security management system ready for action. This system, led by a vice president has the capability to provide company-wide support. The Department of Safety Promotion functions as the compass for the entire Company and at the same time exhibits cross-divisional coordination capability based on the fundamental principle of safety first. The Department of Safety Promotion is working on improving hardware and software used on work sites and developing safety-assist technology in coordination with on-site safety teams.
Safety and sanitation events are organized throughout the year with the participation of members of management, with the labor union and management jointly promoting safety and sanitation activities.
Safety record
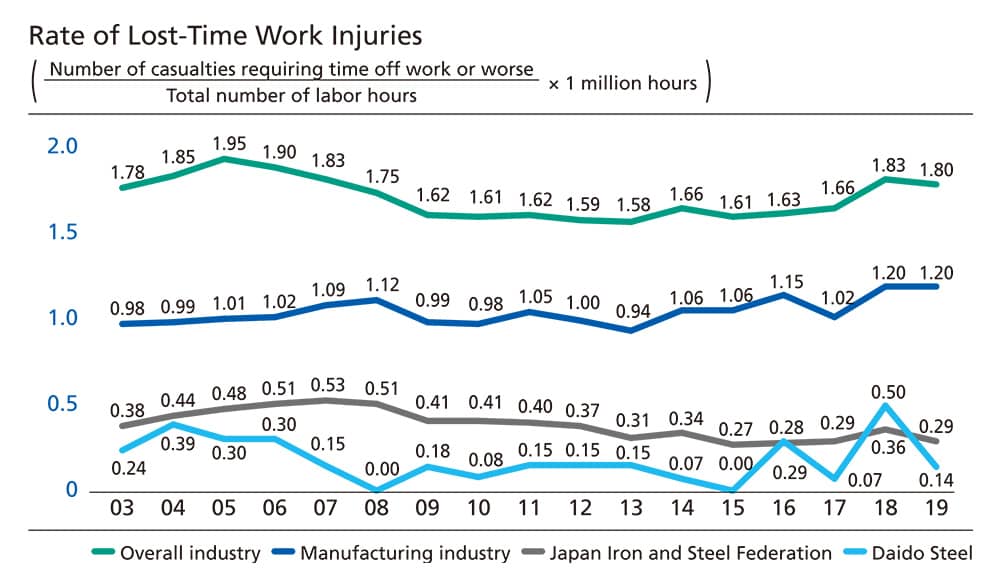
Daido Steel’s rate of lost-time work injuries is lower than the average for the entire industry, and for the steel industry, it has remained especially low and stable (see graph). The Daido Steel Group has an excellent track record, even in the steel industry. However, in 2018, as safety performance deteriorated across the overall industry, the manufacturing industry and the steelmaking industry, the Company’s performance dropped sharply. We are currently working together in a united Company-wide effort to rebuild our safety foundation.