
「なんでもない物に見えるんですが、この団子をつくるのが、なかなか難しいんですよ。」
山内らのプロジェクトにともに参加した大同エコメットの若菜は、開発に至るまでの苦難の道のりを振り返りながらそう語った。革新的な環境リサイクル設備であるPRIMEとは、ひと言で言えばこの“鋼の団子”をつくる設備なのである。
知多工場での特殊鋼製造過程で発生する副産物には、スケールと呼ばれる酸化鉄のかさぶたのようなものと、ダストと呼ばれる金属を含む塵埃がある。これらの副産物をこれまで以上に効率よく再利用するためには、製造工程で集塵機により再びごみとして吸い取られることのない様に、ダストやスケールを粉状ではなく団子状にすることがひとつの大きなポイントであった。この団子をつくるための方法には、副産物をプレスして固めるブリケットという方法と、微粒状の副産物を水で固めて粒状にするペレットという方法の2種類がある。
ここで、山内らは後者のペレットと言う方法を選択した。その選択の鍵となったのが、すでに山内らのプロジェクトチームが注目していたプラントメーカーの設備である。この設備は、通常別々の設備で行う材料の粉砕、粉砕した材料の混錬、そして混ぜたものを転がして団子状に成型していくための造粒過程をすべて1台で行えるという大きなメリットを持っていた。これにより、設備コストやランニングコストを抑えることができる。また、この設備を採用することによって、知多工場で発生する副産物処理をまかなえるだけの高い処理能力が期待できると考えたのである。
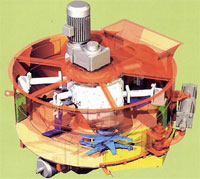 ペレガイア
山内らは、まずこの設備を軸にして新設備の基盤を整えた。あとはスケールやダストを設備にかければよいだけかと言うと、ここからが若菜の語る“難しい”ところである。なにしろこの「ペレガイア」はメーカーにとっても誕生間もない技術であり、ましてや初めて鉄鋼分野の設備を手がけるということで、手探りのスタートだった。しかも、大同では多彩な鋼種を取り扱い、様々な製品を製造しているために、そのプロセスで発生する副産物の種類も多種多様である。この様々な条件の副産物を水と混ぜて、一定の大きさの“団子”を作らなくてはならない。そのためには、ダストとスケールそして、水分の配合率を、想定されるすべての副産物の条件に合わせて試験することが必要であった。若菜らプロジェクトのメンバーは、工場内のあらゆる場所を這いずり回るようにして、サンプルとなる副産物を収集しては配合試験を繰り返した。ニーズの高い新設備に向けての作業であるから、どんなに緻密なこの試験工程にもそれほどのんびりと時間をかけてはいられない。山内を中心にメンバー達は限られた時間の中で必死に答えを探り、ついにスタートから1年足らずで一般鋼、ニッケル系ステンレス、クロム系ステンレスの材料となる3種の“鋼の団子”を作り出すための配合率を見出したのである。 |