
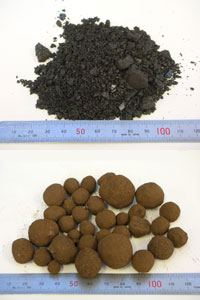 上:造粒前(スケール) 下:造粒後(ペレット) 独自のペレタイジング設備を導入することで、コストを抑えて副産物を団子状にする方法を確立した山内らは、次にその団子の質を高めるための調整を行う。若菜らが幾度もの試験を繰り返し探り出した配合率の数値をもとに、副産物に水分や添加剤を加えて団子状に造粒していくのだが、添加剤にもシビアな要求が課せられた。団子状の原料は、最終的には電気炉に戻される。そのためには、造粒後、生産ラインまでの運搬に耐えうるだけの強度が必要となるのだ。
強度を上げることだけを考えれば、極端な例を挙げればセメントのようなものを混ぜればよいということになる。しかしながら、山内らがつくる“鋼の団子”は飽くまでも原材料として電気炉にかけられるもの。強度を保つためとはいえ、無駄に添加剤を加えてしまえば、生産工程で再びスラグと呼ばれる副産物を生み出すことになってしまう。例えこの副産物を生み出してしまっても、大同にはこれを路盤材などに再資源化し、活用する技術がすでにあるのだが、とはいえ添加剤が混入していることによって、電気炉で無駄な電力を消費するというデメリットは残る。無駄な電力を消費すればCO2排出にもつながり、ひいては地球環境への悪影響という最も避けたい事態へとつながる。そのため、設備が稼動を開始した現在でも、少量で条件に合った“鋼の団子”を実現できる添加剤、固形剤を徹底的に模索し続けている。
また、必要な条件にあう団子を作り出すためには、添加剤の種類選択と同様に、非常にシビアな水分コントロールが必要であった。まさに土で団子をつくるのと同じ要領である。水分が少なければポロポロと団子が崩れ落ち、水分が多すぎればまた崩れやすい泥団子と化してしまう。こうした状況を防ぐためには緻密な水分コントロールが必要となり、実際に操業を任される若菜たちにとっては頭の痛い問題であった。しかし、新設備では、画期的にして実にシンプルな工程を加えることによってこの問題を見事緩和することに成功している。
「この工程を加えることによって、水分調整がかなり融通の利くものになりました。これがなければ、この設備の成功はなかったといえるかも知れませんね。」
と、若菜は語る。新設備では、造粒の後工程として整粒ドラムを採用している。若菜が語るように、重要な工程ではあるがそのメカニズムは実に簡単なもので、団子を入れたドラム缶を回転させ、文字通り造粒した団子をもう一度転がしてその粒を整えるというものである。しかも、山内は偶然にしてこの重要な機能に出会ったという。
「プラントメーカーで、試験を行っているときにどうしたら整った形状の団子を作れるかと考えていたんです。その時に偶然見つけたのがその場にあった2m弱の小さなドラム管でした。」
これはプラントメーカーが、製品としてではなく実用的な道具として現場で使用していたものであった。山内はそれを見て、突然のひらめきに恵まれたのである。こうして、プラントメーカーと大同エコメットとの出会いに始まり、大同エコメットと山内らの強力タッグによる技術開発と偶然から得たひらめきがひとつとなり、ついに新設備が完成したのである。
|